Fiberglass, Resin and Reinforced Plastics Supplier Since 2010
50000+ tons annually sales
Competitive price
Independent research department
Direct processing plant
Develop more new materials and solutions
Technology-Based Supplier
- Years of experience in fiberglass sales and customer technical support
- Rich fiberglass application technology accumulation
-
Independent research and development of fiberglass modified plastics and its own processing plant
50000+ TONS PER YEAR
1000+ CUSTOMERS
10+ YEARS EXPERIENCE
Choose your product category
Choose your production process
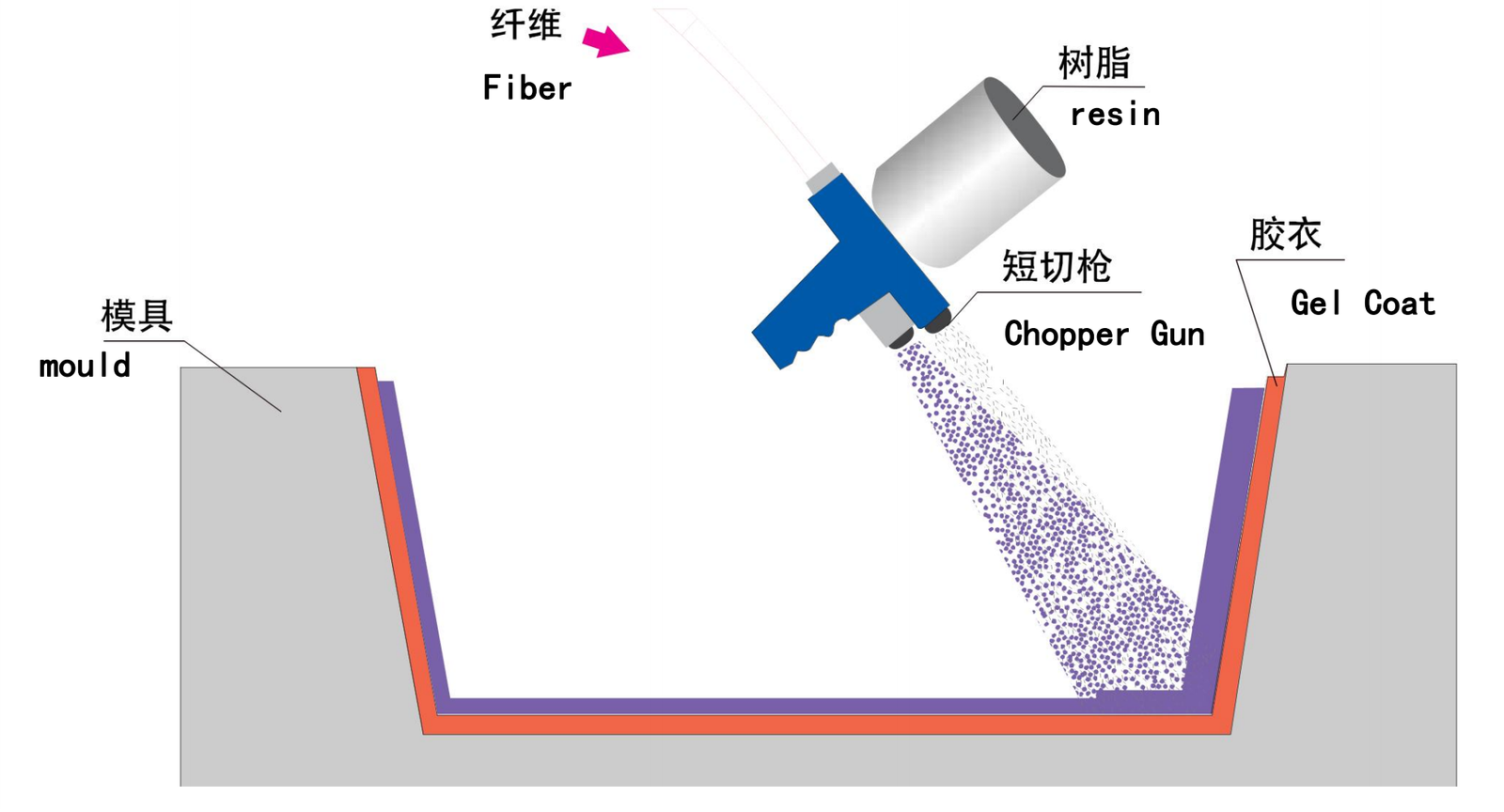
Spray-up Process
The glass fiber is cut and sprayed on the surface of the mold together with the resin by a jet machine

Hand ray-up Process
The mold is evenly coated with release agent and gelcoat resin, and then the reinforcing material is laid. The resin mixed with curing agent is coated with a press roller and a brush to impregnate the reinforcing material and remove bubbles. The laying operation is repeated until the design thickness of the product is reached, and then the molding is solidified under normal temperature or heating condition.
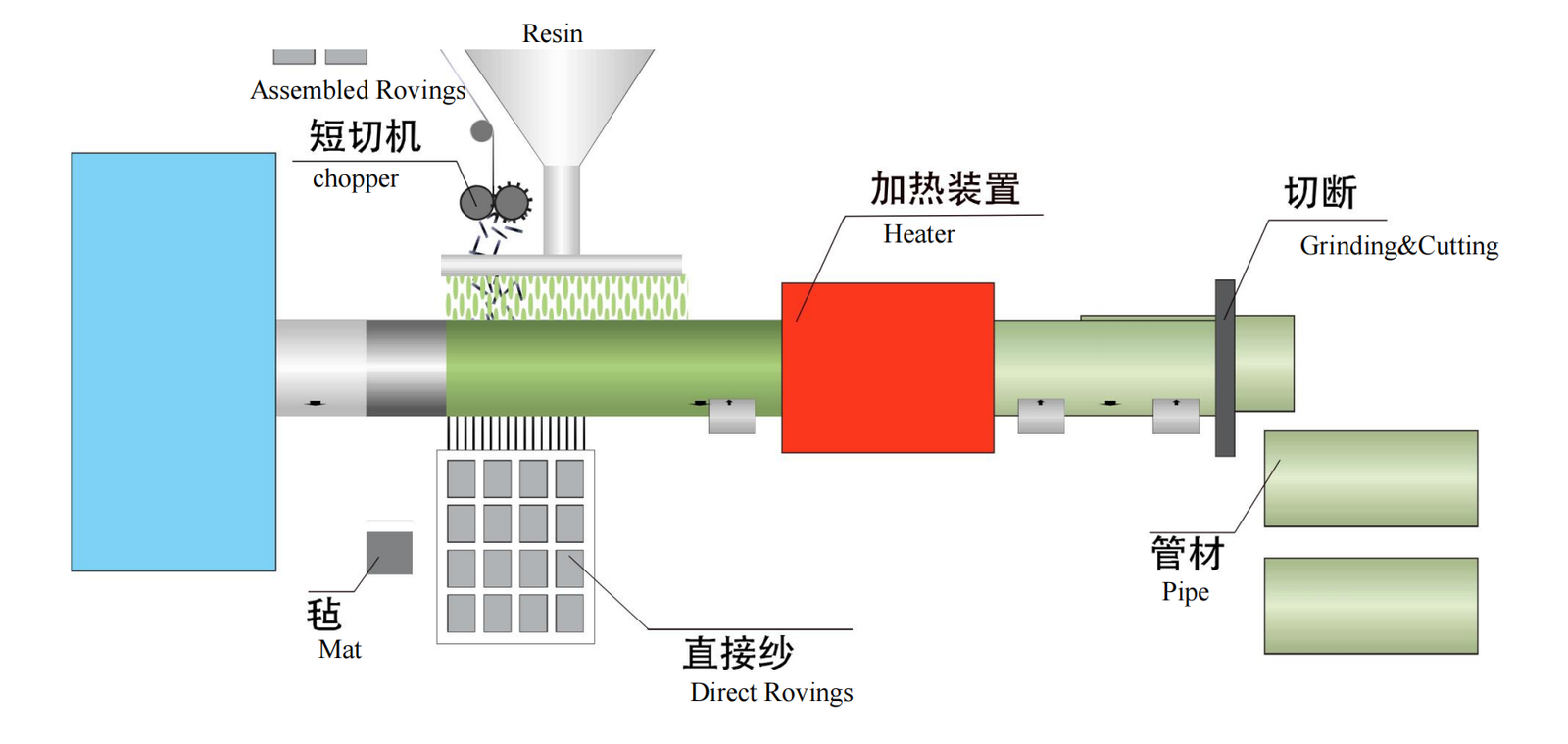
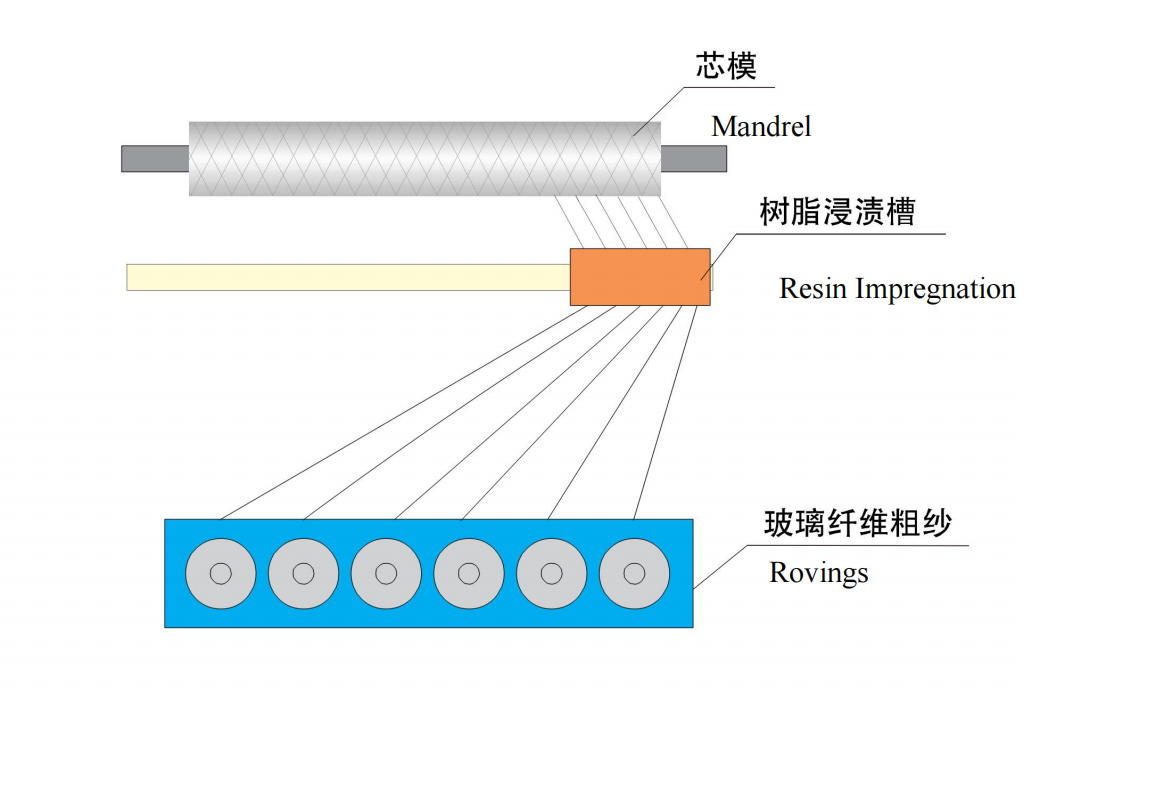
Filament Winding Process
By the continuous back and forth circulation of the steel strip, the fiber winding, composite, sand clamping, curing and other processes are continuously completed on the forward moving inner core mold, and finally the product is cut.
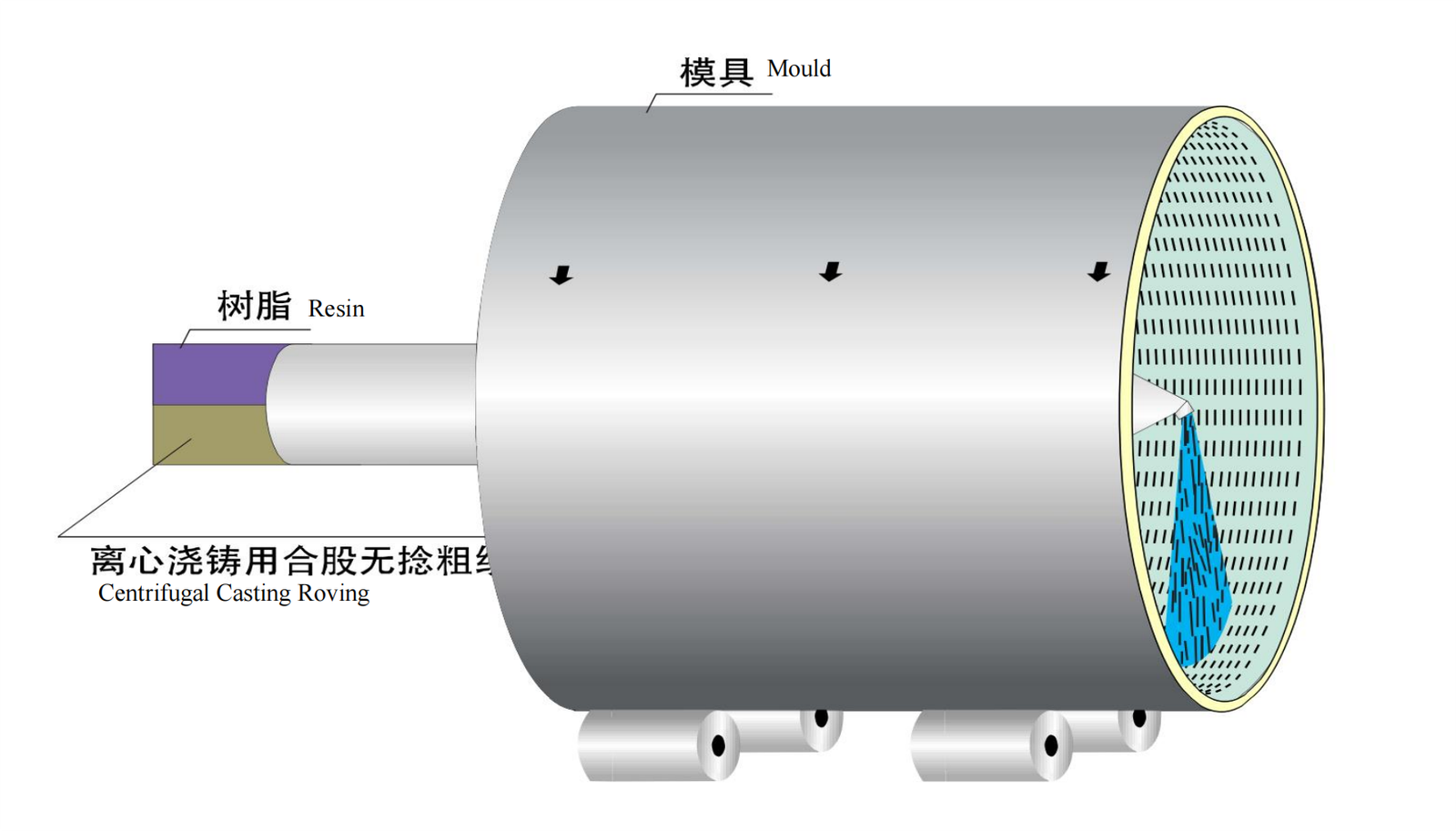
Centrifugal Casting Process
The resin, glass fiber and filler are added to the rotating mold in a certain proportion, and the material is compacted and solidified by centrifugal force generated by high-speed rotation.

Pultrusion Process
The roving,mats or other fabrics are pulled through a resin impregnation bath and then into a heated die using a continous pulling device. The final products are formed under high temperature and high pressure conditions.
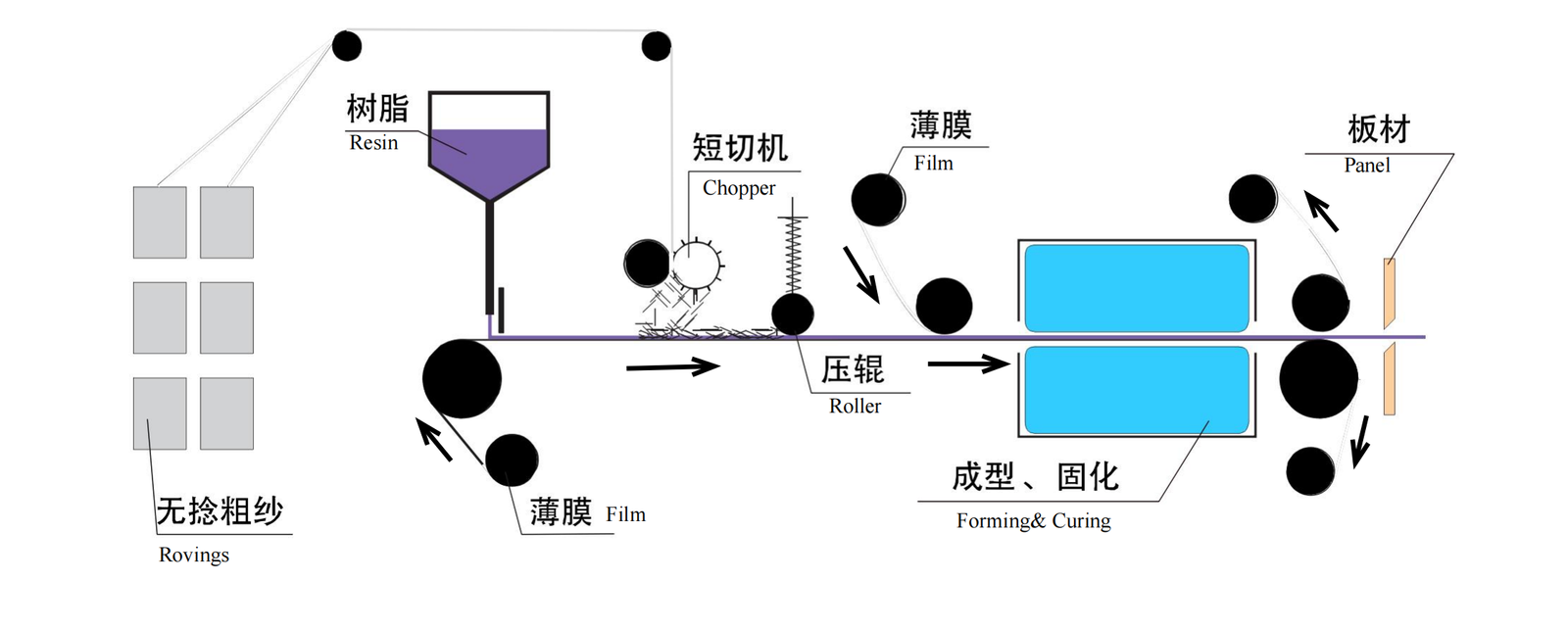
Continuous Panel Molding Process
The roving,mats or other fabrics are pulled through a resin impregnation bath and then into a heated die using a continous pulling device. The final products are formed under high temperature and high pressure conditions.

SMC Process
The resin paste formed by mixing the resin and additives is added to the lower film, and then the twisting roving is cut and settled on the resin paste, and then a film is covered on it, and the semi-finished product – sheet molding plastic is compacted.
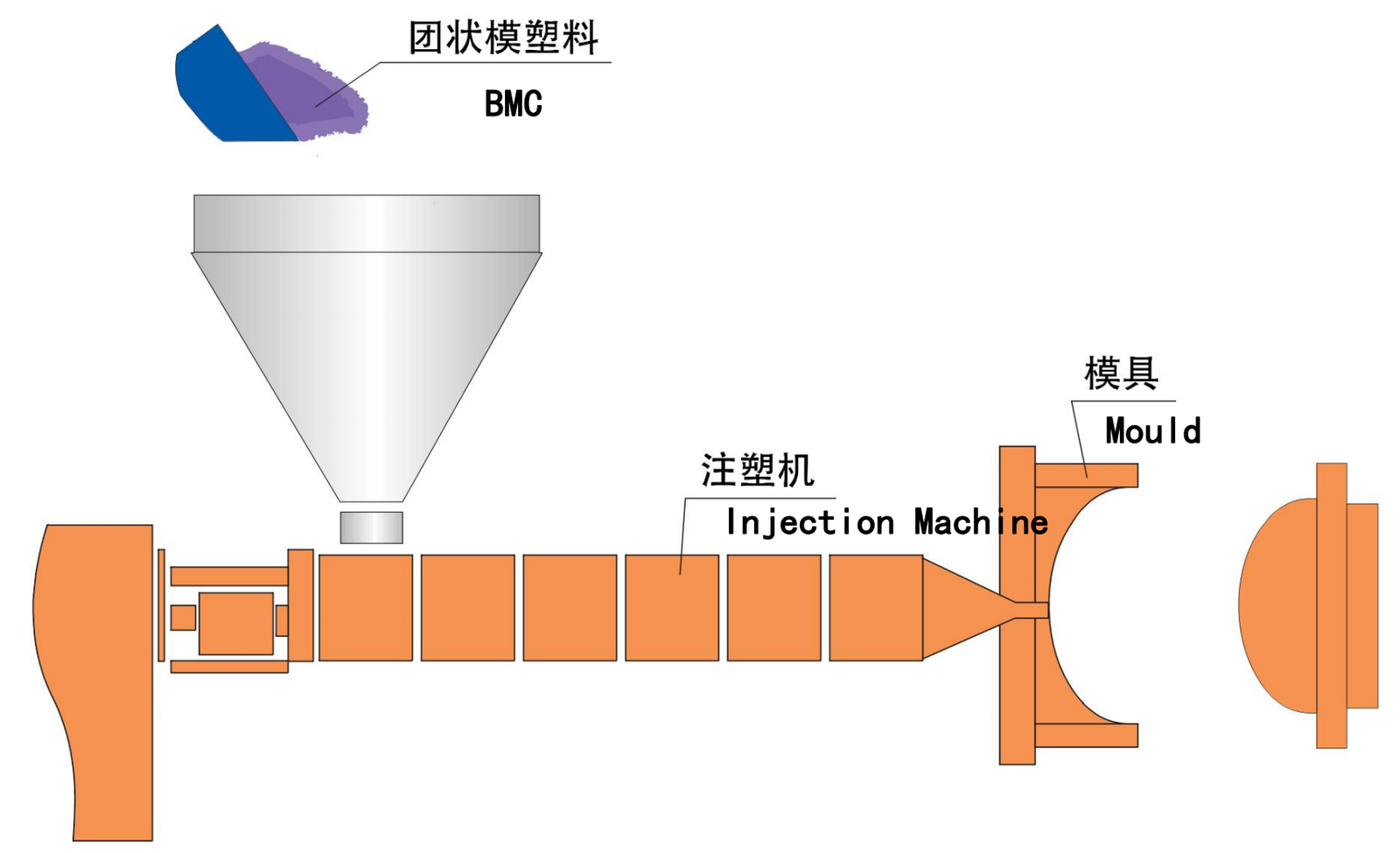
BMC Process
Glass chopped strands, resin, filler and various additives are fully mixed to form the mold plastic, can be injection molding or molding.

LFI Process
The glass fiber is cut to a certain length using a jet and sprayed onto the surface of the mold with isocyanate and polyol. Then the upper mold and the lower mold are closed to react and cure to form the final product.

Weaving Process
Woven fabrics are made on looms with warp or weft reinforcement threads interlaced with each other in varying configurations to give different fabric styles.

Mat Production Process
Assembled roving are chopped to a specified length,and then fall onto a conveyor randomly.The chopped strands are bonded together by either an emulsion binder or a powder binder.after drying,cooling and winding,a chopped stand mat is formed.
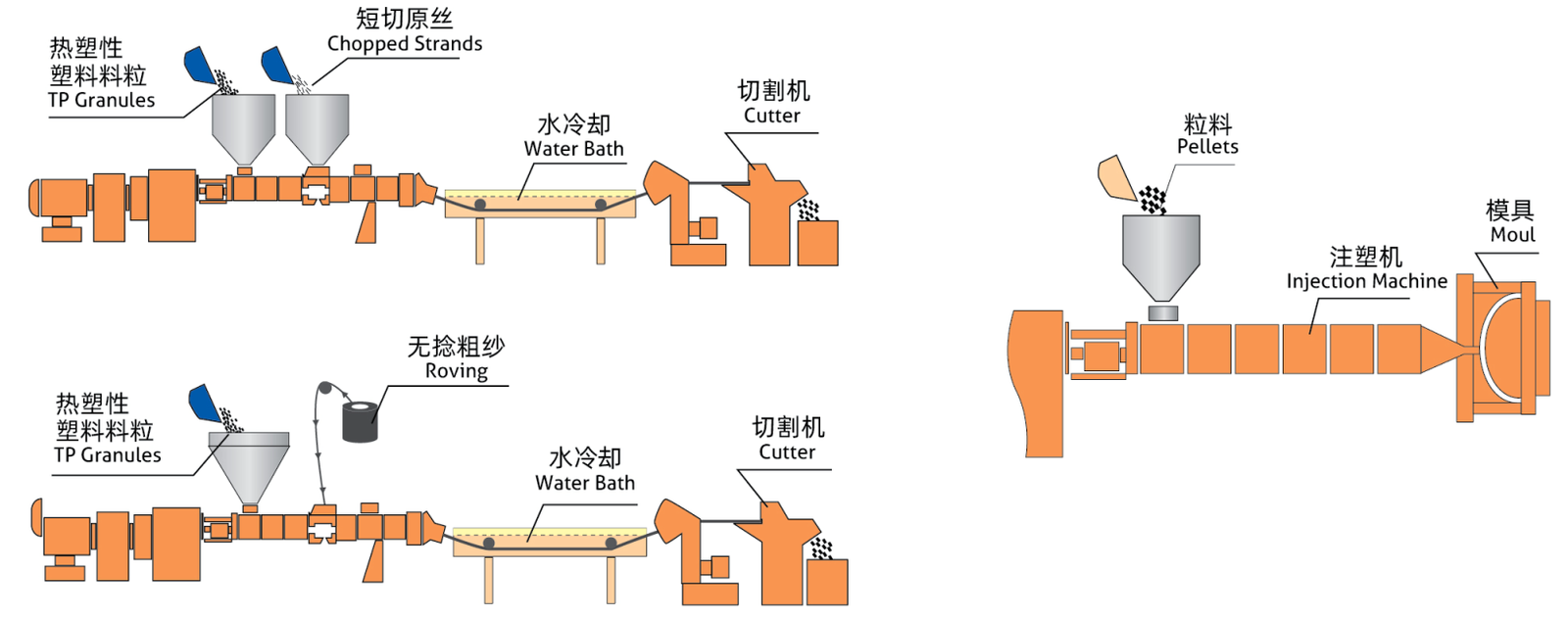
Extrusion and Injection Process
The reinforcements(glass fiber roving or chopped strands) and thermoplastic resin are mixed in an extruder. After cooling, they are chopped into reinforced thermoplastic pellets. The pellets are fed into an injection molding machine to form finished parts.


LFT Process
LFT-D
Polymer pellets and glass roving are all introduced into a twin-screw extruder where the polymer is melted and compound is formed. Then the molten compound is directly molded into the final parts by injection or compression molding process.
LFT-G
The thermoplastic polymer is heated to a molten phase and pumped into the die-head. The continuous roving is pulled through a dispersion die to ensure the glass fiber and polymer impregrated fully and to get consolidated rods. After cooling, the rod is chopped into reinforced pellets.

GMT Process
Generally two layers of reinforcing mat are sandwiched between three layers of polypropylene, which is then heated and consolidated into a semi-finished sheet product. The semi-finished sheets are then heated and molded by stamping or compression process to make complex finished parts.

CFRT Process
A molten mixture of polymer resin and additives is obtained through an extruder. The continuous filament roving is dispersed and impregnated by pulling through the molten mixture. After cooling, curing and coiling, the final material is formed.

Texturizing Process
The roving is introduced to the texturizing machine(air jet), which breaks the surface fibers at random under the effect of compressed air. That gives the roving a bulkier appearance. Then, the texturized roving is wound into a bobbin.
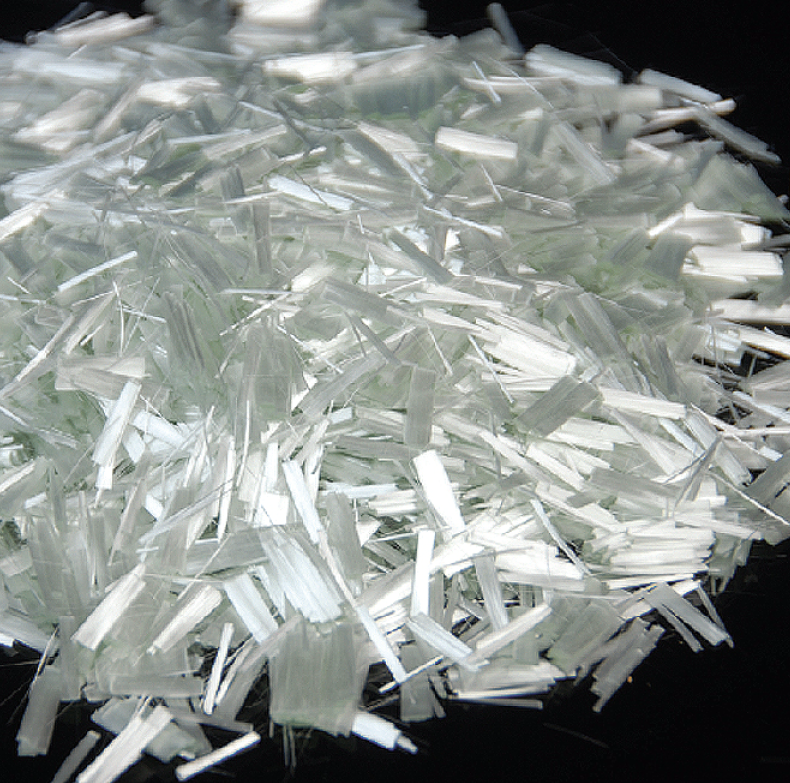
Reinforcements for Gypsum
The slurry is prepared by mixing gypsum powder with other fillers. Then fiberglass is added into the slurry. The slurry is laid on the conveyor for further drying and cutting to form the final sheet.
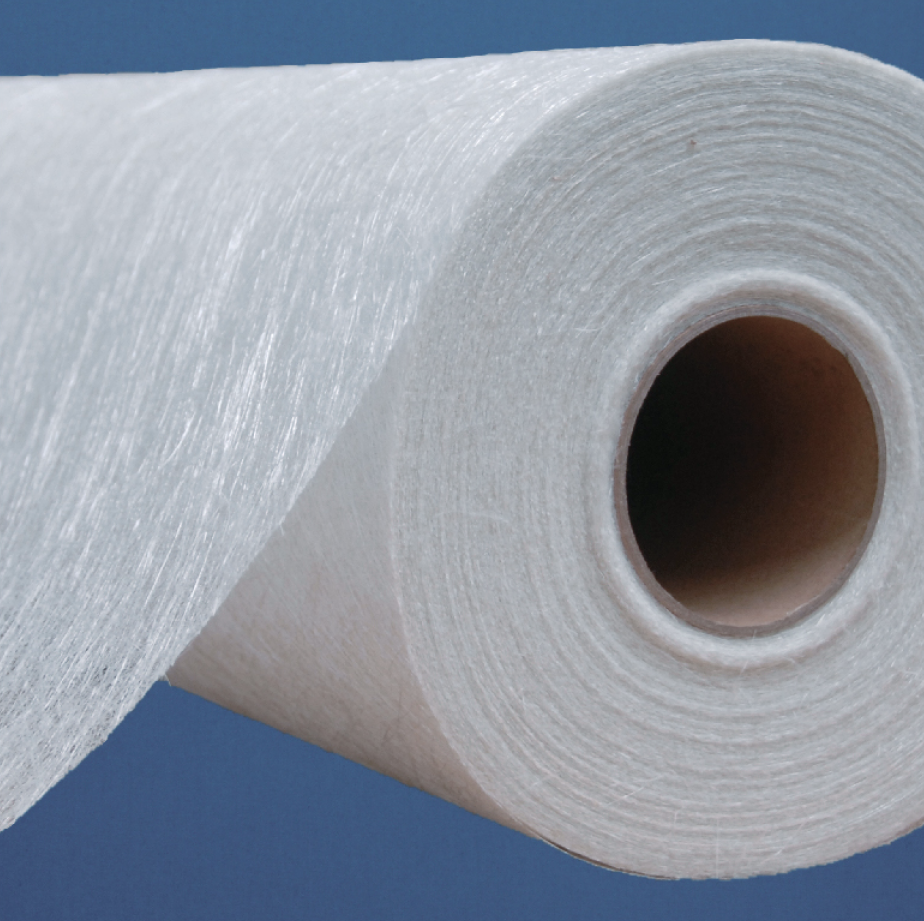
Automotive Headliner Molding Process
PU foam sheets, fiberglass or fiberglass chopped strand mats and non-woven polyester fabrics are bound by a binder and laminated to form automotive headliners.